In the rapidly evolving stonemasonry industry, staying at the forefront of technological advancements is crucial for growth and maintaining a competitive edge. Embracing automation and streamlining business practices are essential steps for stonemasons, setting the stage for sustained long-term success.
In the stone industry context, automation encompasses not only the use of technology to produce and deliver goods with minimal human intervention but also the advancements of Industry 4.0 that enable machines to connect and communicate with one another. This integrated approach of Industry 4.0 allows for the centralised control of the production line, eliminating the need for programming at each individual machine. By streamlining operations and enhancing coordination, automation optimises efficiency and precision across the entire manufacturing process for stonemasons.
Embracing Automation: It’s Not Daunting, Support is Available:
Stonemasons encounter a unique set of challenges that demand specialised solutions with automation, it is essential to tailor approaches to each situation. Each stone masonry factory operates with a diverse mix of machinery and equipment, making it crucial to consider these variations when designing solutions that optimise efficiency and effectiveness.
The good news, with the advanced software available many different types of machines can be centrally managed and brought together to produce the best outcome for the business without having to purchase an entire new production line.
A recommended automation strategy is to first seek advice on the best set-up for your unique stonemason business and the machinery you have, these types of services provide businesses with a clear implementation roadmap, ensuring every piece of equipment is tailored to specific operational needs. CDK Stone can work with stonemasons to produce the best automation structure for their unique business. “Our tailored approach carefully considers the opportunities for each stonemason, taking into account their unique requirements and determining the next steps to begin their journey toward automating their stone processing goals.” said Jonathan Height Joint Managing Director at CDK Stone.
Automation Process
In the stonemasonry industry, automation enhances the fabrication process through advanced tools and technologies. CDK Stone’s automation process is structured around three key stages: capture, create, and produce.
- Capture: This stage involves gathering precise measurements, photographs, dimensions, and edge profiles on site.
- Create: In this phase, the captured data is used to create detailed drawings for the automation line. This includes converting DXF files into a unified CAD drawing and digitising the visualisation of your production requirements, such as book matching.
- Produce: The final stage involves automatically programming each machine to optimise production and run time. Including managing all processes in the factory and efficiently planning the production flow.
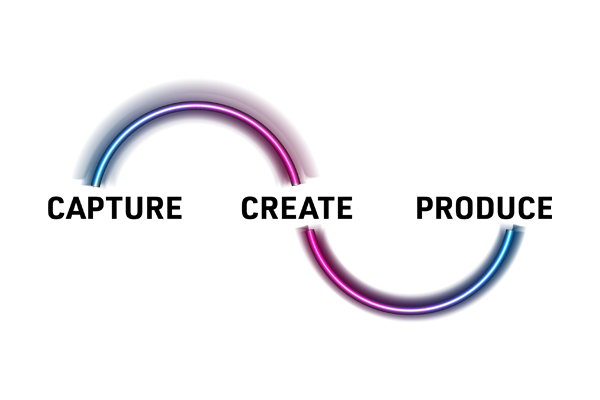
Effective stone processing software is essential in this automation process. It provides tools for drafting, templating, production management, inventory control, design and construction. By streamlining and managing each step through automation, stonemasons can achieve precise and consistent results, making their workflow more efficient and reliable.
A Simple Start to Success
Automation ideally covers the entire stone production line, but significant efficiency gains can be made with specific technologies like the LT3Raptor Laser Templater and Taglio Slab Vision Scanner. These tools reduce waste and the need for re-cutting, offering a seamless entry into automation and saving time on each job from the outset.
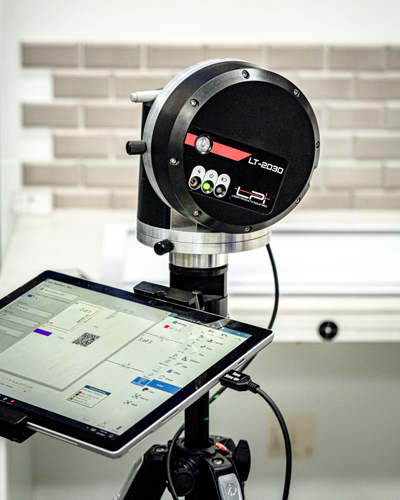
The LT3Raptor software from Laser Product Industries streamlines the templating process with its Templating Intelligence and cloud-based management hub. It allows quick additions of features like sinks and backsplashes and enables sending photos, and CNC-ready files directly from the job site to the office, reducing the time needed to produce fabrication-ready files.
The Taglio Scanner, new to the Australian market, is invaluable for both newcomers to automation and established firms. It revolutionises slab assessment and measurement, ensuring accuracy and maximising material use particularly for high-value materials. By capturing intricate details, it provides a simple and accurate solution to vein matching materials helping reduce waste and allow for pre-customer sign-off on specific stone pieces, enabling stonemasons to achieve outstanding results without increasing their team size or resources. The scanner also enables a library of stocked slabs with full colour and veining detail, for quick reference when selecting slabs for projects..
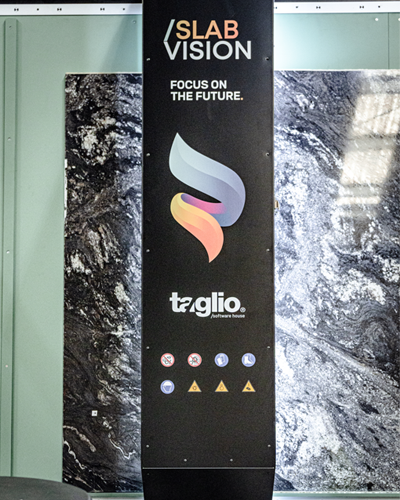
Benefits of Automation:
Increased Efficiency
Automating tasks that were traditionally performed on the factory floor allows businesses to expand production without increasing labour costs. Transitioning these responsibilities to an automated office function, companies can overcome challenges associated with traditional CNC-machine operators who program directly on the factory floor. In a tight labour market this shift not only streamlines operations but also frees up skilled workers to focus on more complex tasks, enhancing overall productivity.
Safer Practices
Automation in stone masonry factories improves safety by reducing the likelihood of human error and limiting the need for manual intervention. Additionally, it provides a reliable and consistent approach to stone fabrication, allowing for a set process that can be refined and improved over time. This continuous enhancement not only boosts safety, but also ensures the workflow becomes increasingly efficient.
Control
Automation optimises every stage of the production process, guaranteeing consistent quality and minimising the chance of defects. This leads to superior stone finishes and greater customer satisfaction.
Flexibility and Expansion
CDK Stone offers flexible software integration, including modular solutions like SeKON Software. Businesses can adopt these modules in phases, allowing for gradual technology adoption without a full upfront investment. This phased approach helps manage costs, ensures a smooth transition, and allows time for training and process integration.